Gas turbine diagnosability at varying operating points.
1 Introduction
Since the beginning of their practical application in the decade of the 1940’s, gas turbine engines (GTE) have proven to be very powerful machines. In the last decades, the development of GTE has increased to inconceivable limits and its usage has extended to various areas such as civil and military aviation, electric energy generation, natural gas compression, and propulsion for land and maritime vehicles [1-3].
GTE are quite complex machines with very high operation parameters like temperature, pressure, and rotation speed and improper maintenance can provoke a catastrophic event. Because of these reasons, condition monitoring systems for GTE are extensively used. These systems are capable to monitor actual condition of the engine, identify the kind and place of a possible fault, predict its possible changes, and therefore reduce the risk and the economic impact of a serious failure or an unexpected engine stoppage [4].
The condition monitoring systems should use all the available information of a diagnosed GTE to cover the majority of its components and systems. Actually, the diagnostic techniques embrace all the primary systems of GTE, such as gas path, transmission, measurement system, fuel system, oil system, starting system, variable geometry systems, etc. Among all these techniques, the algorithms of parametric diagnostics that analyze gas path variables can be considered as essential. They provide a deep vision about the performance of the engine components and they also reveal different mechanisms of degradation. Besides the wear and faults in the gas path, these techniques can also detect malfunctioning of the engine measurement systems.
The gas path diagnostics embraces three mayor components: monitoring of the engine conditions, detailed diagnostics, and prognostic of the remaining life of the engine. The possible faults alter the monitored gas path variables but engine operating conditions (variables that determine the engine regime and ambient conditions) have a higher impact. For this reason, the three components are preceded by a preliminary phase where deviations, between actual and baseline values of the monitored variables are computed. These deviations will be explained in detail further in this paper.
The deviations are computed with random errors and measurement inaccuracy is one of their sources. Since final diagnostic reliability depends on the deviation accuracy and a gas turbine engine should be diagnosed at varying operating conditions, it is of practical interest to reveal how these conditions influence the deviation accuracy. Some investigations accept the hypothesis that the measurement random errors are constant for all engine operating points. In this case, as deviations and their errors have a relative form, the deviation errors increase when the engine descends and all variables go down.
In contrast, in basis of the analysis of real data-based deviations, we consider that their errors do not practically depend on operating points [10]. This is partly explained by the fact that, apart from measurement errors, the deviations have other and greater error components [5, 9].
On the basis of a gas path model, this paper analyses the influence of operating points on diagnostic reliability for both described error hypotheses. Additionally, using real data-based deviations, the paper tries to answer what the hypothesis is most likely.
The paper is structured as follows. A detailed explanation of the gas path model is presented in Section 1. Next, Section 2 summarizes the approach to fault recognition by a detailed description of the diagnostics process. Then, Section 3 describes in more details the two error hypotheses and their influence on diagnostic reliability. The hypotheses are verified on real data in Section 4. Finally, Section 5 presents a discussion of the results obtained.
1. Gas Path Model
A thermodynamic model of GTE can afford a lot of
information useful for diagnostics that would be very difficult to
obtain from a real engine. It is called thermodynamic because in
basis of the thermodynamic laws, the model calculates the variables
in the gas path from the air inlet until the output. The model
determines how monitored gas path
variables
depend on engine operating conditions
(control variables such as rotation speed or fuel consumption and
ambient conditions: air pressure and temperature). In the other
hand, this model can simulate the degradation of each component of
the engine. The vector of state parameters
is included for describing an engine health condition. A vector
corresponds to an engine normal state, while a vector of fault
parameters
shifts a little the performance maps of engine components
(compressor, combustion chamber, turbine, etc.) and in this way
allow simulating different deterioration mechanisms and faults.
Thus, the structure of the thermodynamic model, which can be
characterized as nonlinear and component-based, can be given by the
following formula
. (1)
From a mathematical standpoint, model (1) is a result of solving a system of nonlinear algebraic equations reflecting engine operation at steady states.
2. Diagnostic Approach
If a vector
corresponds to a healthy engine, a baseline model can be presented
by an expression
. (2)
Using the thermodynamic model as a baseline, we can calculate for every monitored variable the relative change (deviation)
(3)
between an actual value Yi and a baseline value Y0i.
The deviations are practically free of an
influence of operating conditions and may serve as good GTE
degradation indicators. That is why they are used for detection,
diagnosis, and failure prediction [6-8]. To make the fault
simulation process more realistic, random errors
are included to the simulated deviations. The total deviation is
presented for each monitored variable Yi
as:
. (4)
The random error
for each variable has its own amplitude
.
This error has a normal distribution and 99.7% of its values are
inside the interval
.
To diagnose the engine in a uniform space, to simplify the
description of the faults, and improve the diagnostic reliability,
this deviations are normalized as follows:
.
(5)
The errors
are generated randomly for all monitored
variables according to the multidimensional normal distribution.
The deviations of all monitored variables form
the vector
,
that is considered a pattern. The fault classification will be
presented on the basis of these patterns.
The GTE faults vary considerably and for the
purposes of diagnosis, numerous gas turbine faults are divided into
a limited number q
of classes
.
Each class corresponds to one engine module and is described by its
fault parameters
.
Each class is determined by a representative
sample of the deviation vector , obtained in basis of expression
(5). A totality
of all classification’s patterns is employed to train the used
neural network, multilayer perceptron and is therefore called a
learning set. It is illustrated by figure 1.
Afterwards, to validate the network, an
additional data simple called a validation set is created in the
same way as the learning set .
The only difference between these sets is that another random
numbers are generated for the validation set. The network classifies
each pattern of the set producing
the diagnosis . Comparing
with a known class Dj
for all validation set patterns,
probabilities of correct classification
are estimated for all fault classes. A mean value
of these probabilities characterizes engine diagnosis reliability
(diagnosability).
Fig. 1. Fault classification representation by patterns
3. Influence of operating points
Since the GTE monitored variables (pressures, temperatures, rotation speeds, etc.) strongly depend on an operating point, deviation errors can depend as well. Therefore, it is practically important to determine what happens with the engine diagnosability when the operating point changes.
As shown in [5,9], there are four main sources of errors that affect the deviations. The first source of error is caused by measurement errors in the monitored and registered variables. Second source of inaccuracy is the error of the measured operating variables which are baseline function arguments. The third source is explained by the fact that the baseline function arguments do not include some variables (air moisture, valves positions, etc) that influence a real engine. The fourth (last) source of error is the inadequacy of the baseline function caused by some factors like algorithm and data sample for determining the baseline function in real conditions. All these error sources have a high impact on the final deviations.
In this section, we will focus our efforts in understanding the effects of the first source of error on the diagnosability at different operating points. To this end, eleven operating points given by successive reduction of a compressor rotor speed are analyzed. Point 1 (engine maximum power) is set by the rotation speed 10700 rpm and the speed decreases until 9700 rpm for point 11.
For the purpose of a better analysis, the deviation error from equation (4) can be expressed as a relative error
, (6)
where
is an absolute error.
Using this expression, we will analyze two
schemes of error change along with the operating point. The first
scheme implies that the relative error
does not depend on the operating point i.e. it is constant for all
points. Figure 2 illustrating this scheme shows the behavior of a
monitored variable Y and its errors Δε and εδY
for the eleven analyzed regimes. As can be seen, when the relative
error εδY is constant, the absolute
measurement error Δε reduces along with reduction of a monitored
variable.
Fig. 2. Constant relative error scheme
The second scheme means that the absolute measurement error Δε is constant. Figure 3 illustrates this scheme using the same format as figure 2. It can be seen here and follows from equation 2 that the relative error εδY increases when the absolute error is constant.
Summing up the analysis of figures 2 and 3, it can be concluded that the analyzed schemes result in significantly different errors at varying operating point. Consequently, using an improper error scheme can result in incorrect deviations and diagnostic inaccuracy. Let us now assess how significant this inaccuracy can be.
Using the two errors schemes, the respective
resulting probabilities
were obtained. They are shown in figure 4 against the operating
points. One can see here that the probabilities corresponding to the
error schemes differ a lot. In this way it is of great importance to
know what scheme takes place in reality.
Fig. 3. Constant absolute error scheme
Fig. 4. Behavior of the probabilities
(PD1o - Constant relative errors, learning set;
PD2o - Constant relative errors, validation set;
PD1m - Constant absolute errors, learning set;
PD2m - Constant absolute errors, validation set)
4. Real Data
Now, when we have revealed great influence of the deviation error scheme on the diagnostic reliability, it is important to find out how this error really changes due to operating conditions and what error scheme is more probable. To solve this issue, the present section uses deviations calculated on basis of real data.
Real data-based deviations have been computed for a two shaft free turbine engine for driving a natural gas centrifugal compressor. Its monitored variables were recorded every hour under field conditions.
Figure 5 illustrates the deviations of the exhaust gas temperature presented versus operation time. We can clearly see systematic tendencies: two periods of compressor fouling divided by the point of washing that recovers the temperature. However, random errors are also seen in the deviation plot presented.
Fig. 5. Engine performance degradation due to compressor fouling (exhaust gas temperature deviation)
Given the computed deviations, their errors have been determined using a degraded engine model as described in [7]. Figure 6 shows the deviation errors of the same exhaust gas temperature versus the operation time.
Fig. 6. Errors of the exhaust gas temperature deviation (whole time interval)
The aforementioned degraded engine mode was identified by the least square method using first 2608 data points. That is why the errors computed in this interval are minimal and more accurate. From here we will analyze only the errors of this interval. They are plotted in a greater scale in figure 7.
When an engine operating point goes down, all the monitored variables decrease as well. In this way an absolute variable value shows how high or low the corresponding operating point is. Therefore, to see the influence of the operating point, we can plot the same variable deviation as before, but now versus the monitored variable itself. Such a plot is given in figure 8. As can be seen, an error spread is practically the same for low and high temperatures, in other words, the deviation error does not practically depend on operating points.
The same error distributions plotted for all other monitored variables are given in figure 1A of Appendix I. Observing these plots, one can arrive to the same conclusion: in general, the hypothesis of the deviation errors independent on an operating point seems to be much more probable then the hypothesis of higher errors for low operating points.
Fig. 7. Deviation errors vs. operation time
(first 2608 data points)
Fig.8. Deviation errors vs. monitored variable
Discussion
Clearly, the selection of a proper hypothesis on deviation error distribution will allow us to simulate the diagnostic process with greater exactitude.
Additionally, the accepted hypothesis demonstrates that the diagnostic reliability does not change a lot with the regime (See figure 4). This means that whichever operating point is equally important for diagnostics. The accepted hypothesis confirms the importance of the multi-point option as well.
This hypothesis also proves the manner of forming a fault classification described in [9]. Because the deviation error is independent of operating points, it can be extracted from real date recorded at different operating point and added to fault-induced deviations in class description.
Furthermore, the accepted hypothesis supports the principle of a generalized classification introduced in [11]. It unites fault manifestations obtained at different operational conditions and allows diagnosis under any conditions. The generalized classification is very useful because it drastically simplifies the gas turbine diagnosis because: once formed, this classification is used later without changes. The deviation errors that are independent of operating conditions present an additional justification for applying the generalized classification.
Conclusions
This paper examines two hypotheses for the deviation calculus in the GTE parametric diagnosis. They were analyzed with the thermodynamic model as a basis for calculating the deviation. It was found that the hypotheses result in very different diagnostic reliability that is why it is important to choose the proper hypothesis.
Also, an analysis is presented, in which errors were extracted from real data-based deviations. The plots of these errors have allowed us to choose the most probable hypothesis that the deviation error is constant (independent of operating point).
Not only acceptance of this hypothesis enhances diagnosis reliability, but it also validates some useful principles that make diagnostic algorithms more realistic and vital.
Acknowledgments
The work has been carried out with the support of the National Polytechnic Institute of Mexico (Research project 20131509).
1. Kacprzynski G. A prognostic modeling approach for predicting recurring maintenance for ship board propulsion system [Text] / G Kacprzynski, J.M. Gumina, M.J. Roemer, D.E. Caguiat, T.R. Galie, J.J. McGroarty // Proc. IGTI/ASME Turbo Expo 2001, New Orleans, USA, June 4-7, 2001. − 7p.
2. Kangas L.J. Automated health monitoring of the M1A1/A2 battle tank [Text] / L.J. Kangas, F.L. Greitzer // Proc. USAF Inaugural Engine Condition Monitoring (ECM) Workshop, San Diego, USA, October 21-23, 1997. − 3p.
3. Greitzer F.L. Gas turbine engine health monitoring and prognostics [Text] / L.J. Kangas, K.M. Terrones, M.A. Maynard, B.W. Wilson, R.A. Pawlowski, D.R. Sisk, N.B. Brown // Proc. International Society of Logistics Symposium, Las Vegas, USA, August 30 – September 2, 1999. − 7 p.
4. Lo Gatto E. Gas turbine off-design performance adaptation using a genetic algorithm [Text] / E. Lo Gatto, Y.G. Li, P. Pilidis // Proc. IGTI/ASME Turbo Expo 2006, Barcelona, Spain, May 8-11, 2006. − 10 p.
5. Miro L.A. Mejoramiento en la simulacion de fallas de turbinas de gas [Text] / L.A. Miro, I. Loboda, E. Torres // Memorias del Congreso Nacional de Ingenieria Electromecanica y de Sistemas 2010, Mexico City, Mexico, 8-12 noviembre, 2010. − 6 p.
6. Loboda I. An overview of gas turbine health monitoring methods [Text] // I. Loboda // Proc. Latinoamerican Conference of Turbo Machinery, Veracruz, Mexico, October 14-17, 2008. −10 p.
7. Loboda I. Diagnostic analysis of maintenance data of a gas turbine for driving an electric generator [Text] / I. Loboda, S. Yepifanov, Y. Feldshteyn // Proc. IGTI/ASME Turbo Expo 2009, Orlando, USA, June 8-12, 2009. − 12 p.
8. Depold H.R. A unified metric for fault detection and isolation engines [Text] / H.R. Depold, R. Rajamani, W.H. Morrison, K.R. Pattipati // Proc. IGTI/ASME Turbo Expo 2006, Barcelona, Spain, May 8-11, 2006. − 7 p.
9. Loboda I. A more realistic scheme of deviation error representation for gas turbine diagnostics [Text] / I. Loboda, S. Yepifanov, Ya. Feldshteyn // International Journal of Turbo & Jet Engines. – 2013. – Vol. 30, Issue 1. − P. 179-190 (ASME Paper No. GT2012-69368 ).
10. Loboda I. Gas turbine diagnostics under variable operating conditions/ I. Loboda, Ya. Feldshteyn, S. Yepifanov [Text] // International Journal of Turbo & Jet Engines. – 2007. – Vol. 24, Issue 3-4. – P. 231-244 (ASME Paper No. GT2007-28085).
11. Loboda I. A generalized fault classification for gas turbine diagnostics on steady states and transients [Text] / I. Loboda, S. Yepifanov, Y. Feldshteyn // Journal of Engineering for Gas Turbines and Power. − 2007. − Vol. 129, Is. 4. − P. 977-985.
Appendix I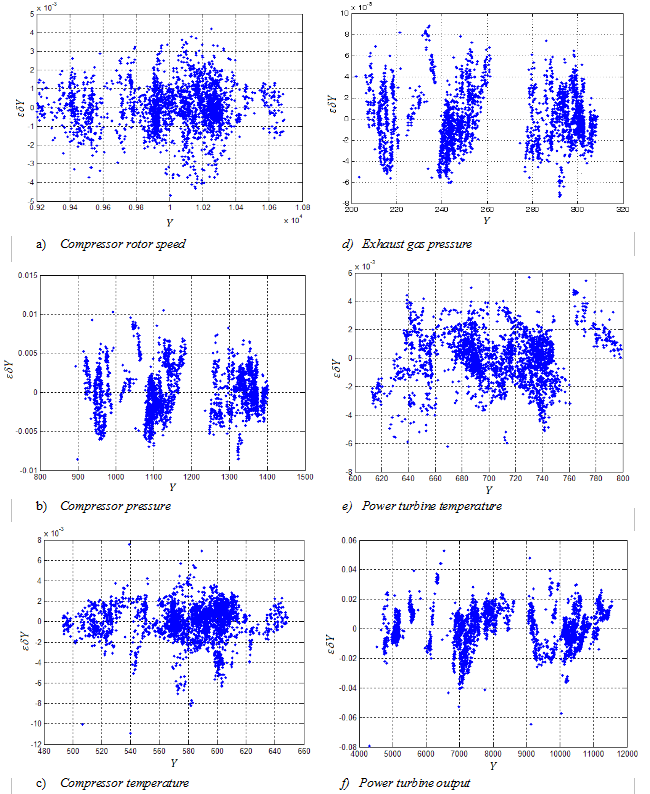
Fig.1A. Deviation errors of all monitored variables